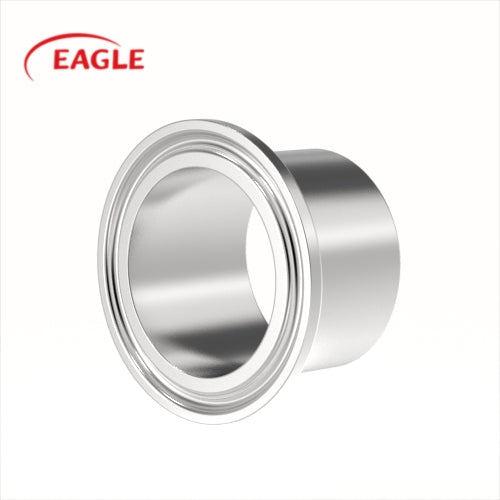
# Fitting and Valve Selection for Optimal System Performance
When designing or maintaining a fluid system, the selection of fittings and valves plays a critical role in ensuring optimal performance. These components are the backbone of any system, influencing efficiency, safety, and longevity. This article explores key considerations for choosing the right fittings and valves to achieve peak system performance.
## Understanding the Role of Fittings and Valves
Fittings and valves are essential for controlling the flow, pressure, and direction of fluids within a system. Fittings connect pipes, tubes, and hoses, while valves regulate or isolate the flow. The right combination of these components ensures seamless operation, minimizes leaks, and reduces energy losses.
### Key Factors in Fitting Selection
1. **Material Compatibility**: Choose fittings made from materials that are compatible with the fluid being transported. For example, stainless steel is ideal for corrosive fluids, while brass is suitable for water systems.
2. **Pressure and Temperature Ratings**: Ensure the fittings can withstand the system’s operating pressure and temperature ranges.
3. **Connection Type**: Select the appropriate connection type, such as threaded, welded, or compression, based on the system’s requirements.
4. **Size and Configuration**: Match the fitting size and configuration to the pipes or tubes to avoid flow restrictions or leaks.
### Key Factors in Valve Selection
1. **Valve Type**: Choose the right valve type for the application, such as ball valves for on/off control, gate valves for isolation, or check valves for preventing backflow.
2. **Flow Characteristics**: Consider the valve’s flow coefficient (Cv) to ensure it meets the system’s flow rate requirements.
3. **Actuation Method**: Decide between manual, electric, or pneumatic actuation based on the level of control and automation needed.
4. **Durability and Maintenance**: Opt for valves with robust construction and easy maintenance features to reduce downtime and repair costs.
## Common Challenges and Solutions
1. **Leakage**: Use high-quality fittings and valves with proper sealing mechanisms to prevent leaks. Regularly inspect and replace worn-out components.
2. **Pressure Drops**: Select fittings and valves with minimal flow resistance to avoid pressure drops and maintain system efficiency.
3. **Corrosion**: Choose corrosion-resistant materials and apply protective coatings to extend the lifespan of components.
4. **Improper Sizing**: Accurately calculate the required size of fittings and valves to ensure they match the system’s flow and pressure requirements.
## Best Practices for Optimal Performance
– Conduct a thorough system analysis to identify the specific requirements for fittings and valves.
– Partner with reputable suppliers to source high-quality components.
– Regularly inspect and maintain the system to address wear and tear promptly.
– Train personnel on proper installation and operation techniques to avoid errors.
By carefully selecting and maintaining fittings and valves, you can significantly enhance the performance, reliability, and safety of your fluid system. Investing in the right components upfront will save time, money, and resources in the long run.
Keyword: fitting and valves